Students Become Blacksmiths for Labor and Working-Class History Course
Posted Mar 02, 2023
While students can learn a lot about history by reading about it, they can also learn a great deal by experiencing it. That’s why Associate Professor of History Anthony DeStefanis is always thinking of creative ways to put his students in the shoes of figures from the past.
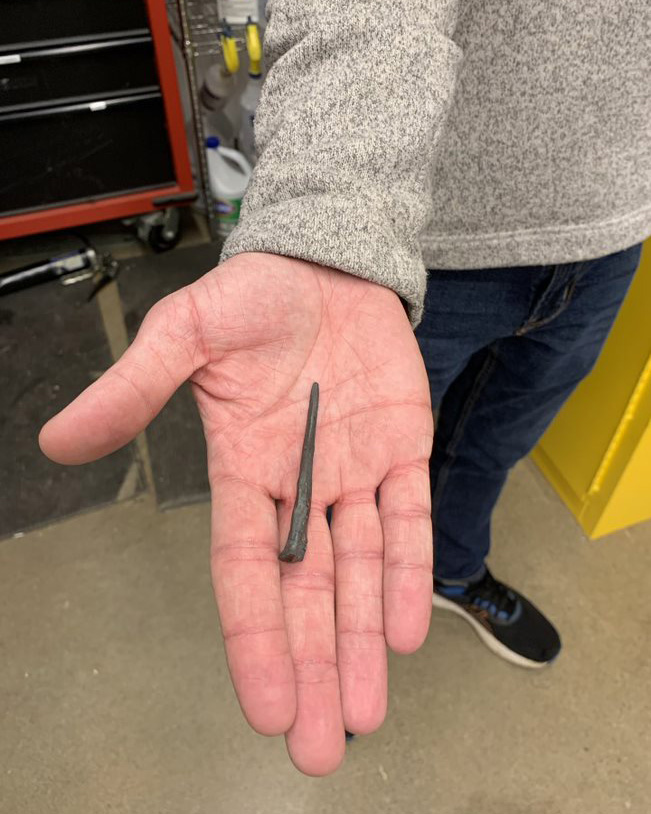
Recently, DeStefanis took his HIST 4400: Riots, Reds, & Riffraff: The History of the Working Class in America class to The Point at Otterbein to learn about what the production of goods looked like before and after the Industrial Revolution.
“This course is about the labor people do in exchange for money. In it, we examine the broad conditions under which work happens, why those conditions looked like they did in the past, and why they look like they do now. The Industrial Revolution fundamentally changed how goods were produced and how labor was organized. In fact, it created an economy that required people to work for a wage that they had little ability to determine,” DeStefanis explained.
“Our visit with Curtis Smith at The Point showed us how blacksmiths made nails before the Industrial Revolution. These tiny fasteners were crucial for the manufacture of many goods and our visit with him reinforces what we have been learning in class about how work changed during the 19th century. The Industrial Revolution wiped out blacksmiths and other skilled artisans and replaced them with factory production in which workers tended machines in highly dangerous conditions for meager wages,” DeStefanis said.
Curtis Smith, Maker Space and laboratory operations manager at The Point, hosted the class in the metal shop to give students the chance to blacksmith. Smith chose to forge a nail — a product whose importance is disproportionate to its size. From sailing ships to shoes, nails have been a crucial component of essential products of all kinds for centuries.
Smith used acetylene gas to produce the heat necessary to forge nails from steel rods, but his other supplies were the tools that blacksmiths used 170 years ago and more: the rod, a hammer, and an anvil.
“Before the Industrial Revolution, every nail a blacksmith made took 1,000 hammer strikes, between heating the metal rod and hammering it against the anvil,” he explained to the students. “A pre-Industrial Revolution blacksmith could make 100-200 nails per hour.”
The American Industrial Revolution began in the 19th century and rapidly created factory-based production. The days of independent skilled artisans like the blacksmith were over. Today one machine can manufacture up to 1,500 nails per minute. The Industrial Revolution also led to the standardization of parts and products.
As Smith explained, before the Industrial Revolution, every product that was made up of more than one part was its own custom design, and to get replacement parts, one would have to go back to the same blacksmith or find one who could replicate the work. Today, you can go to Lowe’s or Home Depot to find standardized parts, including nails.
“The students have been reading Thomas Bell’s Out of this Furnace, a novel that is stunningly realistic in its portrayal of the eastern European immigrants who toiled in Andrew Carnegie’s steel mills during the early decades of Industrial Revolution,” DeStefanis said. “Curtis’ presentation really helped students contextualize what they are reading and learning. They better understand what work looked like before the story Bell tells us unfolded and they have a better appreciation of why workers banded together to demand a better deal in their working lives.”
Senior art history major Rae Rettie volunteered to make a nail using blacksmithing techniques, and said the activity helped her understand the course material better.
“It helps so much. Right now, we’re reading a book called Out of This Furnace, and the main characters are steel workers in the late 1800s. A big part of the book to me is how difficult his job is because they’re not working for much money at all, they’re working 12-hour shifts and sometimes 24-hour shifts, and just how difficult that was to endure,” Rettie said. “It’s one thing to read about it and think, ‘man, I could never work a 12-hour shift doing that,’ and another to try to do it, even if it’s not the exact same job.”
Wesley Engel, a senior history major who also volunteered to forge a nail, agreed.
“It’s easy to read about someone else’s experiences and kind of just move past it — as soon as you’ve gotten done with the paragraph, you kind of put it out of your mind and you focus on the big events that happened to this person instead of the everyday things like manufacturing,” he said. “But it’s hard to understand why these big things happen without learning about all of the small things that made up people’s lives from that time.”